Conducción de repuestos para camiones de engranajes cilíndricos para camiones XCMG HOWO
Conducir engranaje cilíndrico
Debido a que hay muchos tipos de repuestos, no podemos mostrarlos todos en el sitio web. No dude en contactarnos para obtener información específica.
ventaja
1. Le suministramos productos originales y de posventa.
2. Del fabricante al cliente directamente, ahorrándole costes
3. Stock estable para piezas normales.
4. Tiempo de entrega a tiempo, con costos de envío competitivos
5. Servicio postventa profesional y puntual
embalaje
Cajas de Cartón, o según petición del cliente.
descripción
Debido a las características de pared gruesa y delgada de las piezas del engranaje impulsor de la caja auxiliar, la correspondiente cavidad del molde de forja también es relativamente profunda y la pared de la cavidad es más delgada. Durante el proceso de formación, es fácil provocar grietas en la delgada pared del molde, lo que reduce la vida útil del molde. Alto, el costo de las piezas forjadas sigue siendo alto.
Tecnología original del engranaje impulsor de la caja auxiliar.
Figura 1 Engranaje impulsor de una determinada caja auxiliar.
En circunstancias normales, la forja con matriz abierta es el método de forja con matriz más utilizado para piezas de engranajes de transmisión de cajas auxiliares. La ventaja de este método reside en el espesor de la pared del troquel. La fuerza del molde actúa como un amortiguador para asegurar la vida útil del molde, pero la pérdida de material de la rebaba es del 10% al 50% del peso de la forja, un promedio de alrededor del 30%, y el costo del material representa 60% -70% del costo de la forja, por lo que cambiamos este tipo de forjas a producción cerrada.
Análisis de causa
La forja con matriz cerrada consiste en que la pieza en bruto se deforma en una forja en una ranura cerrada mediante recalcado o extrusión. En comparación con la forja con matriz abierta, la parte final formada de la forja con matriz cerrada debe llenarse con la pieza en bruto junto a la pared de la matriz, lo que requiere una mayor resistencia de la pared de la matriz. En el diseño anterior, sólo se consideraba la cavidad de la forja y no se consideraba suficiente la resistencia de la pared del troquel. Sin embargo, es necesario completar la parte que se muestra en rojo en la Figura 2. Después de que la pieza en bruto hace contacto con la pared exterior, se debe continuar presionando la matriz, lo que genera una fuerza excesiva sobre la matriz y la pared de la matriz de forja. Las debilidades, especialmente el filete de raíz (Figura 3), se rompen debido a una fuerza excesiva en la última etapa de formación.
Proceso de forja en caliente cerrado mejorado
Para mejorar la vida útil del molde, para estas piezas forjadas de bridas de paredes delgadas, hemos unificado la consideración de cambiar la estructura del molde, cambiar la estructura general del molde a una estructura de cuerpo y ajustar las ideas de diseño del molde. Para evitar una fuerza excesiva sobre el molde en φ89,6 mm, convertimos la pieza difícil de llenar de φ66,5 mm en una estructura separada y, al mismo tiempo, aumentamos los orificios de ventilación en φ89,6 mm para reducir la asfixia durante el formado. proceso, como se muestra en la Figura 4. Se muestra. Después del cambio, la vida útil del molde ha mejorado significativamente, de las 1500 piezas anteriores a aproximadamente 3000 piezas, pero aún no puede satisfacer las necesidades de la producción in situ, especialmente las necesidades de vida útil del molde de la línea de producción automática.
Volvemos a analizar todo el forjado, y bajo la premisa de no cambiar los materiales utilizados en el proceso de forjado, garantizamos dos puntos para el diseño del troquel de preforjado y del troquel de forjado final: primero, asegurar que la vida del troquel cumple con los requisitos de diseño sin agrietarse; en segundo lugar, la forja. La expulsión del molde es suave y no habrá fenómeno de atasco. Creemos que el espesor de la pared lateral del troquel superior de la forja es pequeño y que la fuerza de impacto en el troquel superior es mucho mayor que la del troquel inferior durante el proceso de formación de la forja. Por lo tanto, la forja está diseñada para girar, es decir, la parte de pared gruesa de la matriz está diseñada en la matriz superior. La parte de paredes delgadas se diseña en el molde inferior, y la parte de paredes delgadas del molde inferior y el anillo exterior de formación se diseñan como un todo, como se muestra en la Figura 5 marcada con el anillo exterior del molde 43. En el proceso de diseño, el diseño previo a la forja es el más crítico y puede reflejar mejor el nivel técnico del diseñador. El preforjado desempeña principalmente una función de separación del material, que puede prepararse para el conformado final del forjado. En el diseño, nos aseguramos de que la pieza preforjada sea lo más gruesa posible y llene la cavidad en la ranura de forjado final, sin reflujo en blanco, para reducir la extrusión posterior de la forja tanto como sea posible, reduciendo la fuerza de conformado. y reduciendo el plegado del forjado. El riesgo resultante.
Una vez realizado el diseño del troquel según la nueva idea, las piezas forjadas están llenas y la vida útil del troquel alcanza los requisitos de diseño. Cuando el molde se utiliza en una prensa de tornillo de estaciones múltiples o de alta energía, la vida útil del molde aumenta más del doble que la original, lo que reduce el costo de forja y reduce la intensidad de mano de obra de los trabajadores.
en conclusión
Este artículo llega a las siguientes conclusiones comparando los diferentes procesos de diseño de moldes de las piezas del engranaje impulsor de la caja auxiliar:
Al diseñar la cavidad de preforjado, es necesario considerar la distribución del material y el modo de flujo de la pieza en bruto durante el proceso de conformado de la forja.
El proceso cerrado de este tipo de engranaje impulsor de ala alta es diferente del proceso cerrado de otros engranajes, especialmente en líneas automáticas de alta velocidad. Debido a que la viga móvil tiene una transmisión relativamente rápida y no puede ser interferida por mano de obra, es necesario considerar completamente cada uno de ellos en el proceso de diseño. El posicionamiento de los pasos de trabajo y la distribución de materiales deben ser precisos, especialmente el diseño de la cavidad de preforjado debe estar preparado para el forjado final.
Para la mayoría de las prensas de alta energía, normalmente sólo hay pasos de recalcado y forjado final, y el diseño del troquel es más difícil. El diseño preferido de la cavidad de forjado final puede reducir la tasa de desperdicio de piezas forjadas y, al mismo tiempo, evitar las deficiencias del agrietamiento fino y fácil de la pared del troquel debido a la estructura del producto, reduciendo así efectivamente el costo de la forja.
El diseño del molde de las piezas del engranaje impulsor de la caja auxiliar tiene un significado de referencia y referencia para el diseño de otros moldes con estructuras similares.
Nuestro-almacén1
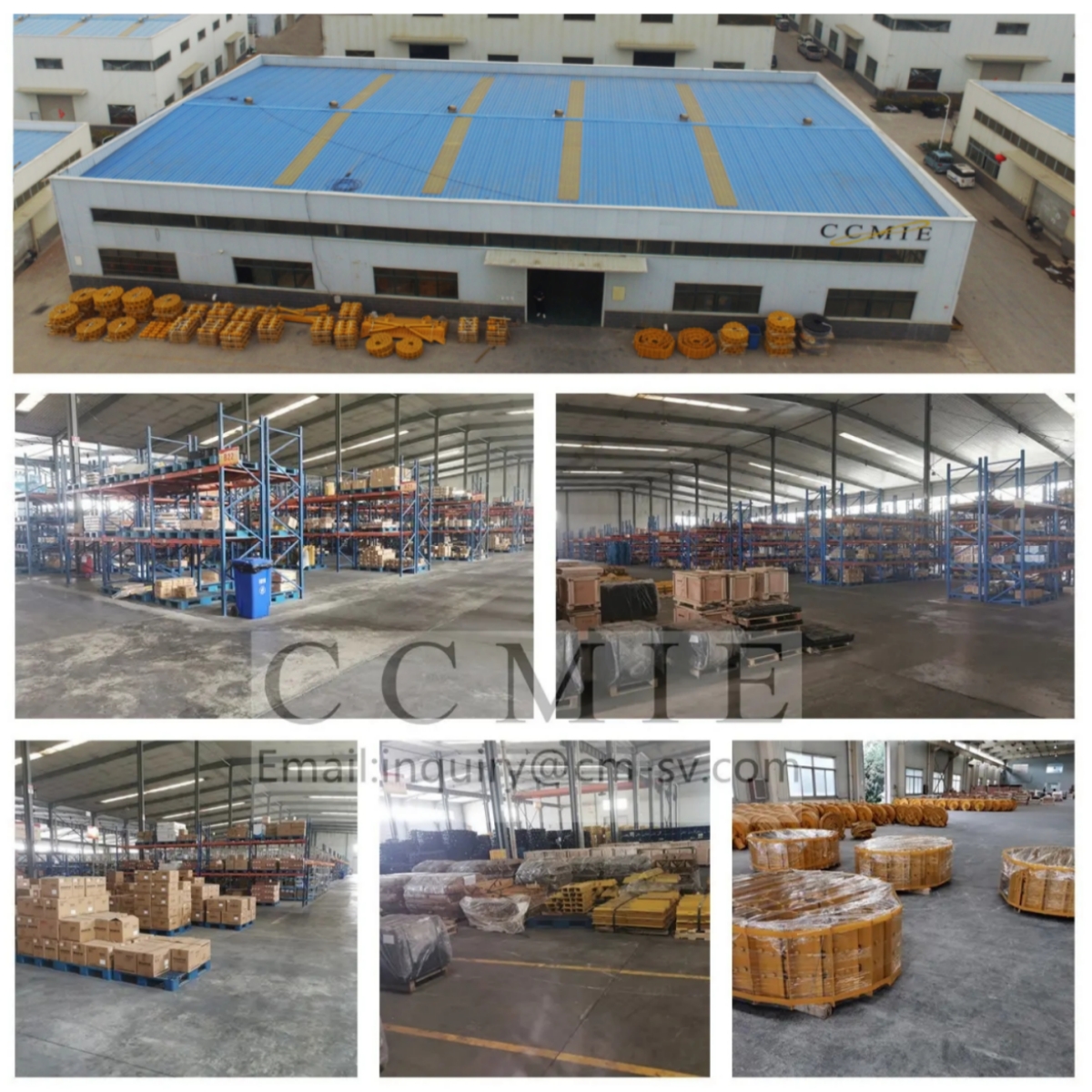
Empacar y enviar

- Elevación aérea del brazo
- Camión volquete chino
- Reciclador en frío
- Revestimiento de trituradora de cono
- Elevador lateral de contenedores
- Pieza de topadora Dadi
- Accesorio barredor para montacargas
- Piezas de niveladora Hbxg
- Piezas del motor Howo
- Bomba hidráulica para excavadora Hyundai
- Piezas de topadora Komatsu
- Eje de engranaje de excavadora Komatsu
- Bomba hidráulica para excavadora Komatsu Pc300-7
- Piezas de topadora Liugong
- Repuestos para bombas de hormigón Sany
- Repuestos para excavadoras Sany
- Piezas del motor Shacman
- Eje de embrague de niveladora Shantui
- Pasador del eje de conexión de la niveladora Shantui
- Eje flexible de control de niveladora Shantui
- Eje flexible de niveladora Shantui
- Kit de reparación del cilindro de elevación de la niveladora Shantui
- Piezas de topadora Shantui
- Eje de carrete de niveladora Shantui
- Eje de marcha atrás de niveladora Shantui
- Repuestos para niveladora Shantui
- Eje de transmisión del cabrestante de niveladora Shantui
- Perno topador Shantui
- Rueda guía delantera de topadora Shantui
- Kit de reparación del cilindro de inclinación de la topadora Shantui
- Engranaje cónico Shantui Sd16
- Forro de freno Shantui Sd16
- Conjunto de puerta Shantui Sd16
- Junta tórica Shantui Sd16
- Rodillo de oruga Shantui Sd16
- Manguito de rodamiento Shantui Sd22
- Disco de fricción Shantui Sd22
- Rodillo de oruga Shantui Sd32
- Piezas del motor Sinotruk
- Carro de remolque
- Piezas de niveladora Xcmg
- Repuestos para niveladoras Xcmg
- Cerradura hidráulica Xcmg
- Transmisión Xcmg
- Piezas del motor Yuchai